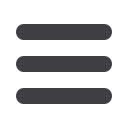
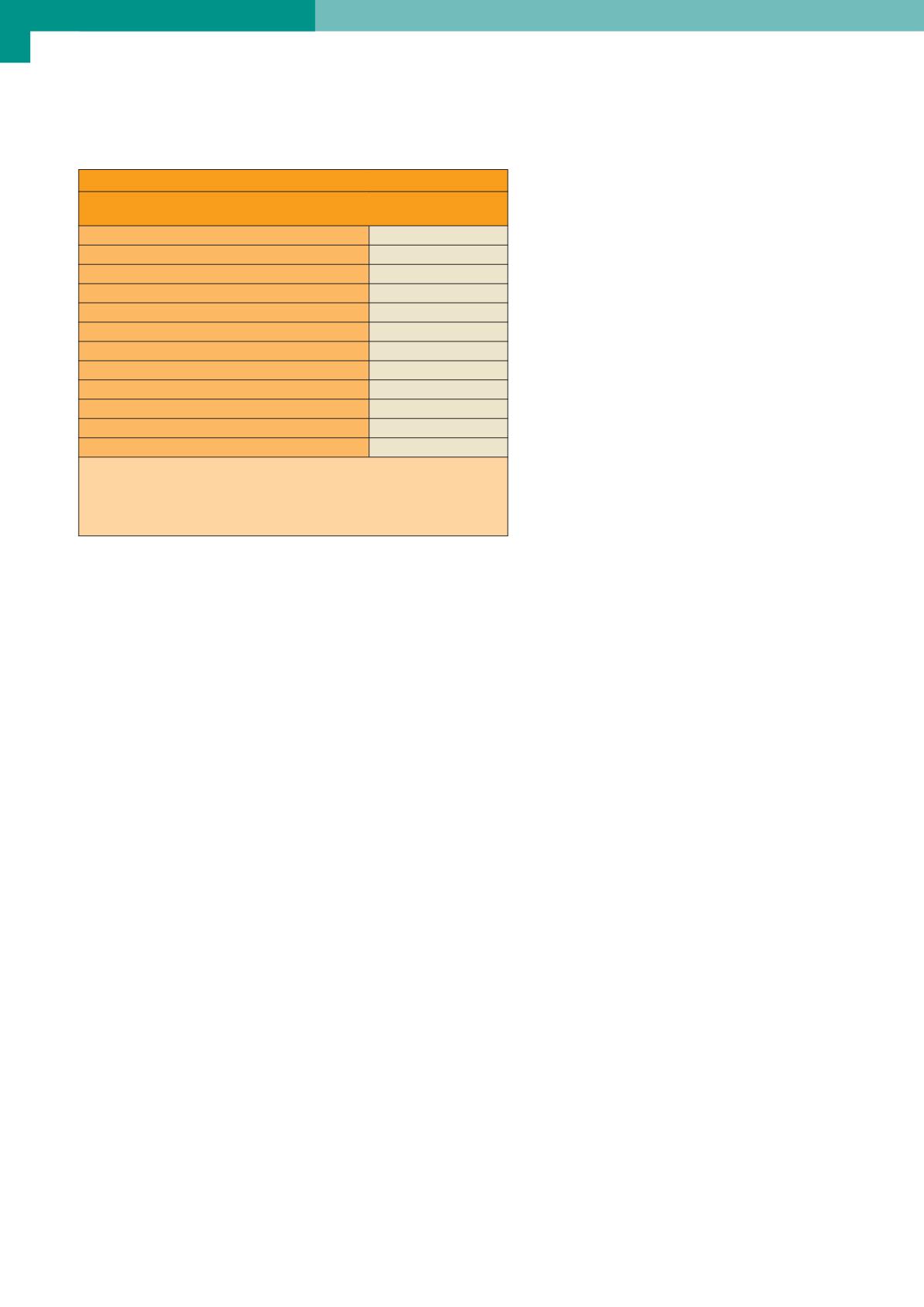
COMPONENTS
EMI PROTECTION
52
- ELETTRONICA OGGI 443 - MARZO 2015
e 1298 offrono una maggiore resistenza ai carburanti idrocar-
burici, agli acidi diluiti e ai fluidi decontaminanti NBC (nucleari,
batteriologici e chimici). La tabella 2 mostra i potenziali di cor-
rosione in millivolt dei metalli e dei comuni materiali per guar-
nizioni EMI, immersi in acqua salata, illustrando le posizioni dei
materiali di riempimento delle guarnizioni nella serie galvanica.
Nello scegliere una guarnizione schermante, il progettista deve
chiaramente considerare anche altre proprietà chiave del ma-
teriale scelto, come l’efficacia schermante, la deformazione pla-
stica, l’intervallo termico e l’invecchiamento, in modo da soddi-
sfare tutti i requisiti applicativi.
Trattamento superficiale
Nella maggior parte delle applicazioni, l’involucro metallico può
essere placcato o verniciato, per migliorarne l’aspetto e impe-
dirne l’ossidazione e la corrosione. Analogamente, le superfici
delle flange dovrebbero essere verniciate, per garantire una
protezione ottimale dalla corrosione. La vernice, tuttavia, deve
essere elettricamente conduttiva per massimizzare l’efficacia
della schermatura, non dovrebbe contribuire alla corrosione
delle superfici delle flange e dovrebbe mantenere una stabilità
meccanica ed elettronica in tutte le condizioni operative. Una
buona aderenza a lungo termine è fondamentale e ciò general-
mente richiede un’adeguata preparazione della superficie della
flangia prima dell’applicazione della vernice.
I componenti della serie Chomerics CHO-SHIELD 2000 sono ri-
vestimenti di uretano a tre elementi con riempitivo in rame, pro-
gettati per impedire la corrosione delle superfici di alluminio in
ambienti marini e molto umidi. Sono disponibili diverse formule,
come i CHO-SHIELD 2001 e 2003, che contengono cromati sol-
ubili che minimizzano gli effetti della corrosione galvanica del
substrato di alluminio. Tutte le varianti contengono additivi che
garantiscono la stabilità elettrica alle alte temperature.
I rivestimenti CHO-SHIELD 2001 e 2003 sono progettati
per essere utilizzati su un substrato di alluminio con
rivestimento cromatizzato (MIL-DTL-5541 Tipo I, Classe
3), preventivamente trattati con CHO-SHIELD 1091 per
favorire l’aderenza.
Lo spessore del rivestimento e la procedura di essicca-
mento hanno un’influenza significativa sul rendimento
delle protezioni dalla corrosione.Un rivestimento umido
di spessore 0,175 mm (7 millesimi di pollice) produrrà
una pellicola essiccata di spessore 0,1 mm (4 millesi-
mi di pollice), che è lo spessore minimo raccomandato
per ottenere un elevato livello di protezione alla corro-
sione e di prestazioni elettriche. CHO-SHIELD presenta
le proprie caratteristiche elettriche ottimali solo dopo
l’asciugatura. Il miglior metodo è un’asciugatura per 2
ore a temperatura ambiente seguita da 30 minuti a 120
°C (250 °F).
In alternativa, il rivestimento può essere fat-
to asciugare per 2 ore a temperatura ambiente e poi per 2 ore
a 60
°C (150
°F), oppure per 7 giorni a temperatura ambiente.
Anche se le procedure alternative di asciugatura riducono la
resistenza alla corrosione, la protezione ottenuta è comunque
valida per un’ampia gamma di applicazioni, in particolare per
apparecchiature utilizzate in ambienti controllati.
Rivestimento secondario
Si potrebbe considerare un’ulteriore protezione dall’umidità, in
presenza di nebbie e spruzzi salini, e quindi per impedire i fe-
nomeni elettrolitici che portano alla corrosione. In applicazioni
aeronautiche, ad esempio, si potrebbe usare una progettazione
del tipo “guarnizione su guarnizione”, illustrata in figura 1. Come
si vede, guarnizioni dello stesso materiale vengono applicate a
ognuna delle flange affacciate, poi ermetizzate ai bordi con un
sigillante non conduttivo, per impedire all’umidità di penetrare
nell’area compresa fra guarnizione e flangia.
Una combinazione “ad hoc”
La corrosione galvanica può avere luogo nei punti di contat-
to fra le flange e le guarnizioni schermanti dopo prolungate
esposizioni a fenomeni bruschi come schizzi e vapori salini, in
particolare se non si presta un’appropriata attenzione alla scel-
ta delle guarnizioni, al trattamento superficiale delle flange e
all’ermetizzazione. Poiché la corrosione è un fenomeno naturale
in cui il metallo si adatta a formare un composto stabile nell’am-
biente, non è possibile impedirla in modo assoluto e definitivo.
Grazie a una appropriata combinazione di guarnizioni scher-
manti, rivestimenti conduttivi ed ermetizzazioni supplementari,
i progettisti possono ridurre al minimo o per lo meno limitare la
corrosione e assicurare una appropriata efficacia della scher-
matura elettromagnetica per tutto il periodo di vita dell’appa-
recchiatura.
Q
Tabella 2 –Metalli emateriali per guarnizioni EMI nella serie galvanica
Potenziali di corrosione di alcuni metalli emateriali comuni per guarnizioni
EMI (dopo 15 minuti di immersione in soluzione al 5%di NaCl a 21 °C)
Materiale
Ecorr vs SCE* (millivolt)
Argento puro
-25
Elastomero riempito d’argento
-50
Maglia di Monel
-125
Elastomero riempito di rame placcato argento
-190
Elastomero riempito di alluminio placcato argento
-200
Rame
-244
Nickel
-250
Rame-berillio placcato stagno
-440
Maglia di acciaio ricoperta in rame placcato stagno
-440
Alluminio*
-730
Elastomero riempito di alluminio placcato argento
-740
*Elettrodo di riferimento in calonelano. Leghe di alluminio approssimativamente da
-700 a 840 mV rispetto SCE in 3% NaCl.
Mansfield, F. and Kenkel, J.V., “Laboratory studies of galvanic corrosion of aluminium
alloys”. Galvanic and Pitting Corrosion – Field and Lab Studies, ASM STP 576, 1976,
pp. 20-47