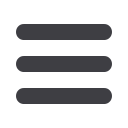
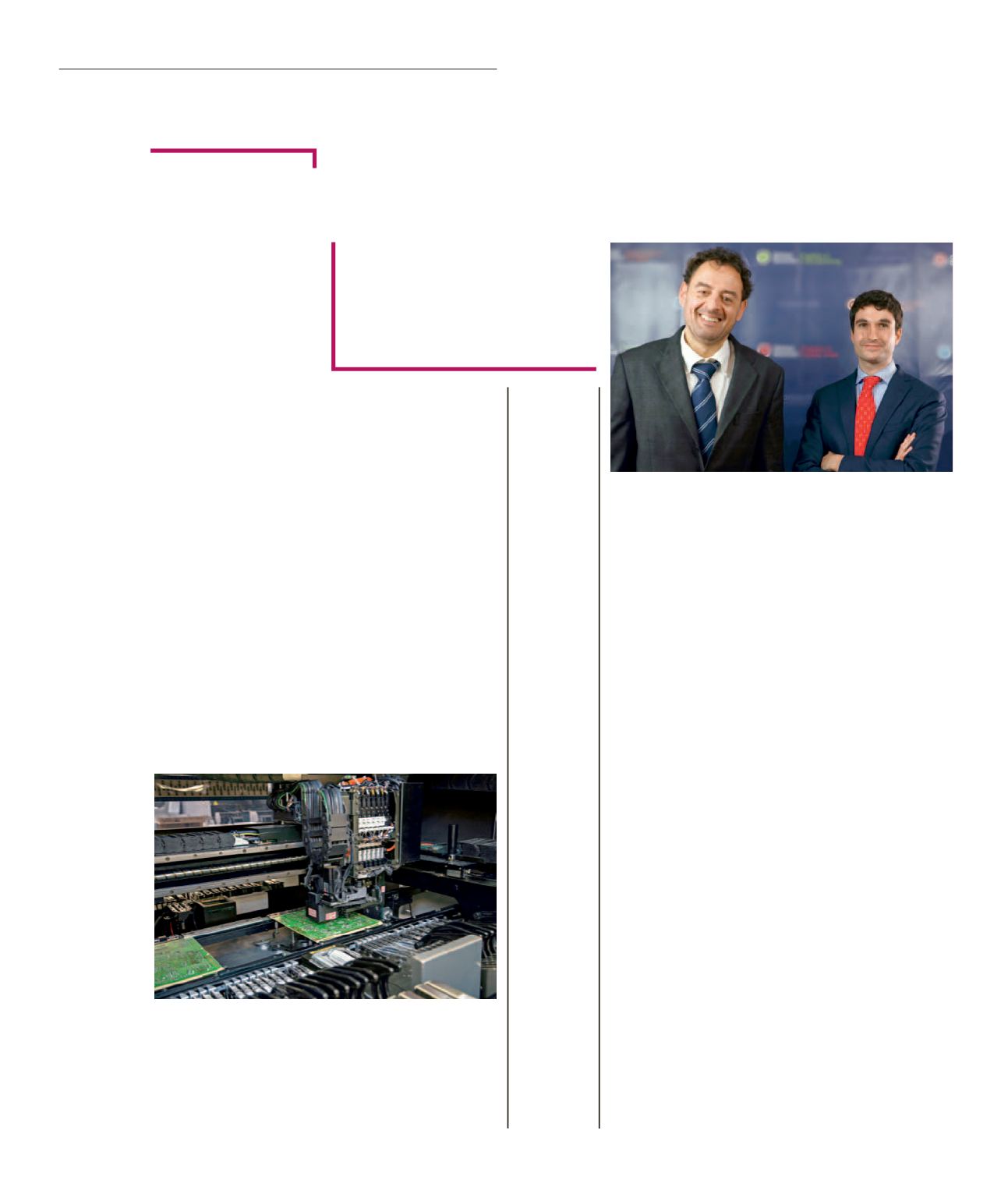
EON
EWS
n
.
607
-
APRILE
2017
22
S
apere l’esatta posizione in
azienda di 6mila codici di pro-
dotto diversi, i materiali e com-
ponenti utilizzati e il tempo
impiegato per la produzione di
ciascuno è un po’ come avere
la carta d’identità di ogni singo-
lo pezzo. Questi sono i risultati
della fabbrica 4.0; risultati cui è
approdato il
progetto MES che
la friulana
Tecnest
ha svilup-
pato per il colosso dell’elettro-
nica
Elemaster.
Il caso è stato
presentato nell’ambito dell’ulti-
mo Global Logistics & Supply
Chain Summit svoltosi a Benti-
voglio (Bo).
Grazie all’applicazione della
soluzione J-FLEX MES (Ma-
nufacturing Execution System)
di Tecnest, azienda di Udine
specializzata in soluzioni orga-
nizzative e informatiche per la
gestione della Supply Chain e
delle Operations, Elemaster ha
migliorato l’efficienza e la visibi-
lità sui processi.
“Il lavoro svolto ci ha permesso
di ottimizzare i tempi ciclo e di
poter individuare i colli di botti-
glia lungo il processo di produ-
zione, così da aumentare l’effi-
cienza, migliorare la visibilità e il
controllo in tempo reale e ridur-
re il time to market”, ha spiegato
Giovanni Cogliati, sales mana-
ger di Elemaster, società con
quartier generale a Lomagna
(Lc) che, con mille dipendenti
e 185 milioni di fatturato, è tra
le maggiori società ODM-EMS
in Europa
.
Specializzata nella
progettazione, sviluppo e rea-
lizzazione sia di schede elettro-
niche sia di dispositivi completi,
integrati con la produzione di
componenti custom e la produ-
zione di PCB, Elemaster ha in
portafoglio i principali attori glo-
bali nei settori ad alto contenuto
tecnologico come l’elettromedi-
cale ed healthcare, il settore fer-
roviario e dei trasporti, l’avionica
e la difesa, l’high-tech mobility,
il settore industriale ed energy.
Ottimizzare
la produzione
La necessità era quella di ot-
timizzare i processi di produ-
zione per rispondere in modo
più efficace ed efficiente alle
richieste del mercato. “Il recen-
te processo di trasformazione
trasversale che l’azienda ha
messo in atto sia in termini di
internazionalizzazione,
con
l’apertura degli stabilimenti in
USA, India e Cina per essere
più vicini ai nostri clienti, sia di
rivoluzione dei sistemi infor-
mativi, ci ha portato a rivedere
anche i processi di produzione
per ottimizzare tempi e costi
e ottenere migliore visibilità e
controllo su tempi, materiali e
risorse utilizzate”, ha aggiunto
Cogliati
. “
Siamo un’azienda
complessa, vendiamo ogni
anno più di 6 milioni di prodotti
finiti divisi su circa 6mila codici-
articolo diversi e gestiamo in
termini di materie prime più di
150mila articoli
.
Per gestire tut-
ta questa complessità e rispon-
dere alle esigenze del mercato,
oltre agli strumenti tecnici e alle
competenze manageriali inter-
ne, avevamo bisogno di affidar-
ci a un partner specializzato e
a soluzioni software avanzate
per la gestione dei processi di
produzione”.
Da qui la scelta di Tecnest e
l’implementazione della solu-
zione J-FLEX di Tecnest. “Il
progetto MES si è focalizza-
to sul dispatching dei piani di
produzione, sulla raccolta dati
in tempo reale, sulla gestione
e controllo degli avanzamenti
in reparto e sulla gestione del-
la tracciabilità e della qualità.
Tutto questo anche attraverso
un’integrazione in real-time del
nostro sistema J-FLEX con
l’ERP, i sistemi di automazione,
le macchine di produzione e di
test di Elemaster per permette-
re di convogliare in tempo reale
tutti i dati relativi alle quantità
prodotte e ai tempi impiegati.
E, in caso di errore, avvisare i
responsabili per metterli nelle
condizioni di intervenire con
azioni correttive”,
ha spiegato
Fabrizio Taboga, project ma-
nager di Tecnest.
“Un aspetto
fondamentale del progetto è la
gestione della tracciabilità e rin-
tracciabilità in produzione. Attra-
verso l’utilizzo di codici univoci e
la definizione di opportune unità
di gestione logistica dei mate-
riali, il sistema genera legami di
tracciabilità dalle materie prime
al prodotto finito e viceversa,
con riferimento sia ai lotti di ma-
teriale utilizzato, sia alle risorse
impiegate nel processo”.
Attualmente,
attraverso 200
postazioni di reparto e una cin-
quantina di palmari, Elemaster
è in grado di conoscere l’esat-
ta posizione di ogni singola
scheda elettronica presente in
azienda e quanto tempo è stato
necessario per produrla
. “
Un
risultato – ha concluso il Sales
Manager di Elemaster – che si
è concretizzato in una migliore
visibilità e controllo in tempo
reale dei processi e in un au-
mento delle performance pro-
duttive, con l’eliminazione degli
sprechi e la riduzione dei costi
nell’ottica di un miglioramento
continuo”.
A
LESSANDRO
N
OBILE
Per Elemaster
la fabbrica
digitale è una realtà
Grazie al progetto MES sviluppato
dalla friulana Tecnest una delle
maggiori società ODM-EMS in
Europa ha migliorato l’efficienza
e la visibilità in tempo reale sui
processi di produzione
Una fase di
produzione
(Fonte: Elemaster)
FABRIZIO TABOGA
(a sinistra), project manager di Tecnest e
GIOVANNI COGLIATI
(a destra), sales manager di Elemaster
A
TTUALITÀ