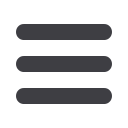
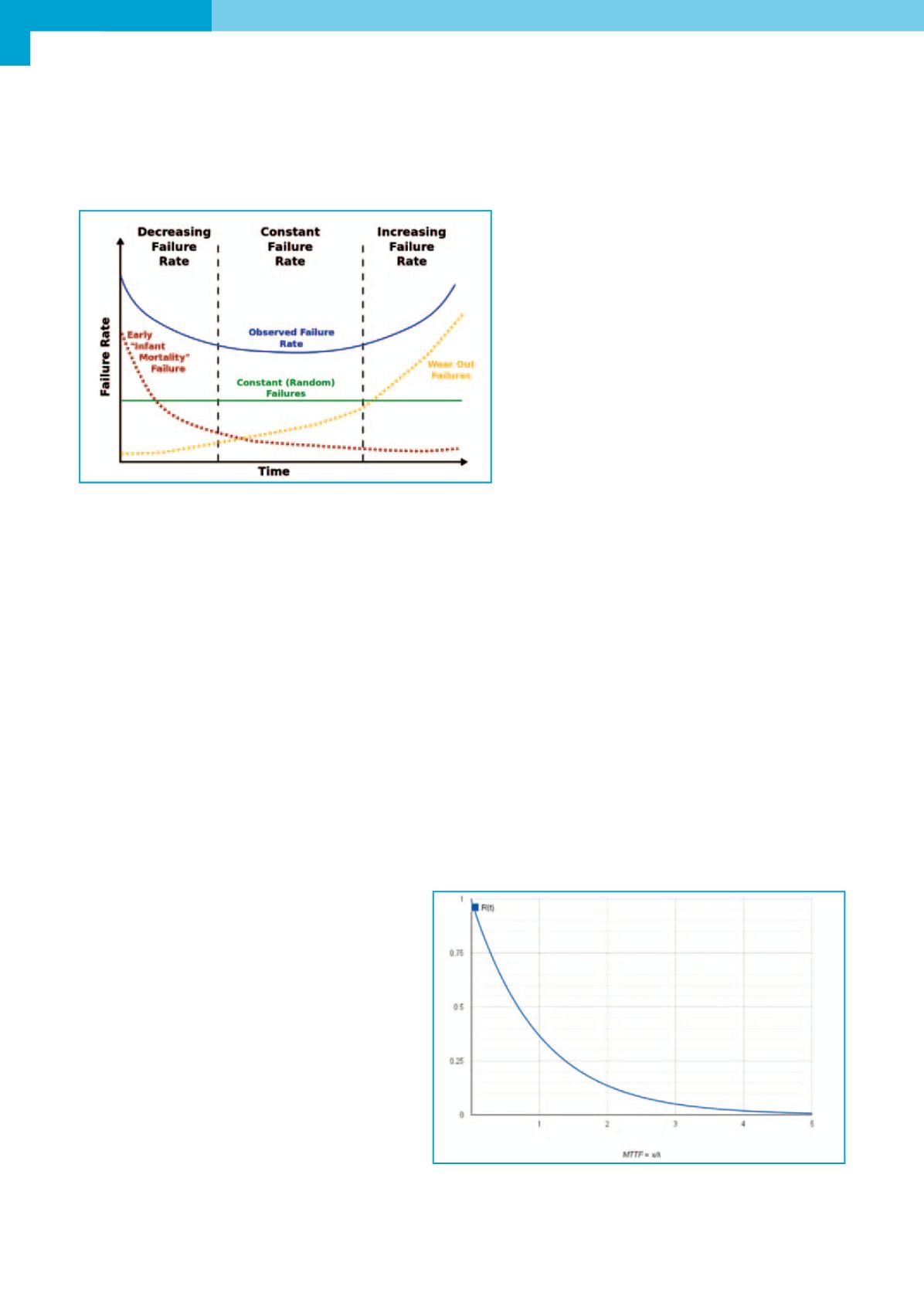
POWER
RELIABILITY
36
- ELETTRONICA OGGI 456 - SETTEMBRE 2016
La metodologia MIL richiede l’uso di numerosi parametri per i
differenti componenti e prevede l’applicazione di sollecitazioni
di potenza e tensione, mentre la metodologia seguita da Telcor-
dia prende in considerazione un numero inferiore di parametri
del componente e tiene conto di altri dati desunti da test di labo-
ratorio, dai risultati delle prove di burn-in e dai test sul campo.
Con l’approccio MIL è possibile ottenere i dati relativi all’MTBF
mentre l’approccio basato su Telcordia produce i dati relativi
al FIT (Failures In Time), dove un FIT equivale a un guasto per
miliardo (10
9
) di ore di funzionamento (equivalente a circa
114.115 anni).
Per l’utilizzo dei database e delle tecniche cui si è appena
fatto riferimento è necessario fare alcune ipotesi – come ad
esempio che il progetto sia perfetto, tutte le sollecitazioni siano
conosciute, il funzionamento avvenga all’interno dei range
nominali previsti, ogni singolo malfunzionamento provochi
un malfunzionamento totale e i database siano attuali e
validi – che spesso non risultano corrette.
In ogni caso questa metodologia è quella che richiede
meno tempo e se utilizzata in modo coerente per differen-
ti progetti, può fornire un’indicazione circa l’affidabilità
relativa delle varie topologie e approcci di progettazione,
piuttosto che sull’affidabilità assoluta.
Per contro la valutazione è il metodo più accurato per
prevedere il tasso di guasto, a fronte di un maggior onere
in termini di tempo e risorse. Essa prevede di sottoporre
un congruo numero di unità finite a un test di durata
accelerato a elevata temperatura: per l’esecuzione di tali
test i fattori di sollecitazione sono di intensità crescente e
controllati in maniera accurata.
Uno di questi collaudi, noto come test HALT (Highly Acce-
lerated Life Test), prevede il collaudo di un certo numero
di prototipi nel maggior numero di condizioni operative
possibili, con diversi cicli di temperatura, tensioni di
ingresso, carichi di uscita e altri parametri che hanno un
impatto sulla durata. Il test HALT è una prova a fatica, il
cui obbiettivo è appunto mettere alla prova la resistenza
di un componente, una scheda PCB, un sotto-insieme o un
prodotto finito attraverso l’applicazione di sollecitazioni di
elevata intensità per un numero ridotto di cicli o di solleci-
tazioni di minore intensità per un numero maggiore di cicli.
Un secondo metodo, denominato test HASS (Highly Acce-
lerated Stress Screen), è una tecnica utilizzata per indivi-
duare guasti latenti che non sono stati rilevati da altri tipi
di collaudo quali ESS (Environmental Stress Screening),
burn-in e altri. Il collaudo HASS utilizza sollecitazioni di
intensità superiore rispetto a quelli previsti dalle specifi-
che iniziali ma che comunque il progetto, in base ai risul-
tati del test HALT, è in grado di supportare.
Poiché le sollecitazioni previste dal test HALT sono più
rigorose rispetto a quelle utilizzate nei collaudi di tipo
tradizionale, tale metodologia permette di ridurre il tempo
richiesto per individuare eventuali problemi legati al processo
produttivo. Gli specialisti che si occupano di affidabilità posso
quindi apportare le modifiche atte a impedire il verificarsi di
successivi malfunzionamenti sul campo, con tutti i vantaggi
che ciò comporta.
Anche se è possibile l’osservazione sul campo, risulta molto
difficile da implementare in quanto è praticamente impossibile
controllare tutti le condizioni in cui un alimentatore si trova ad
operare: da qui la difficoltà di effettuare un’analisi accurata
delle cause.
Le sollecitazioni che influenzano l’affidabilità
di un alimentatore
La durata di un alimentatore è influenzata da tre diversi tipi
di sollecitazioni: termiche, meccaniche ed elettriche. Un pro-
Fig. 1 – La curva “a vasca da bagno” riporta il tasso di guasto in funzione del
tempo durante le tre fasi del ciclo di vita di un prodotto: mortalità infantile, vita
utile e usura
Fig. 2 – In questa curva è riportata la probabilità di corretto funzionamento di un
componente in funzione del tempo