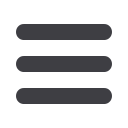
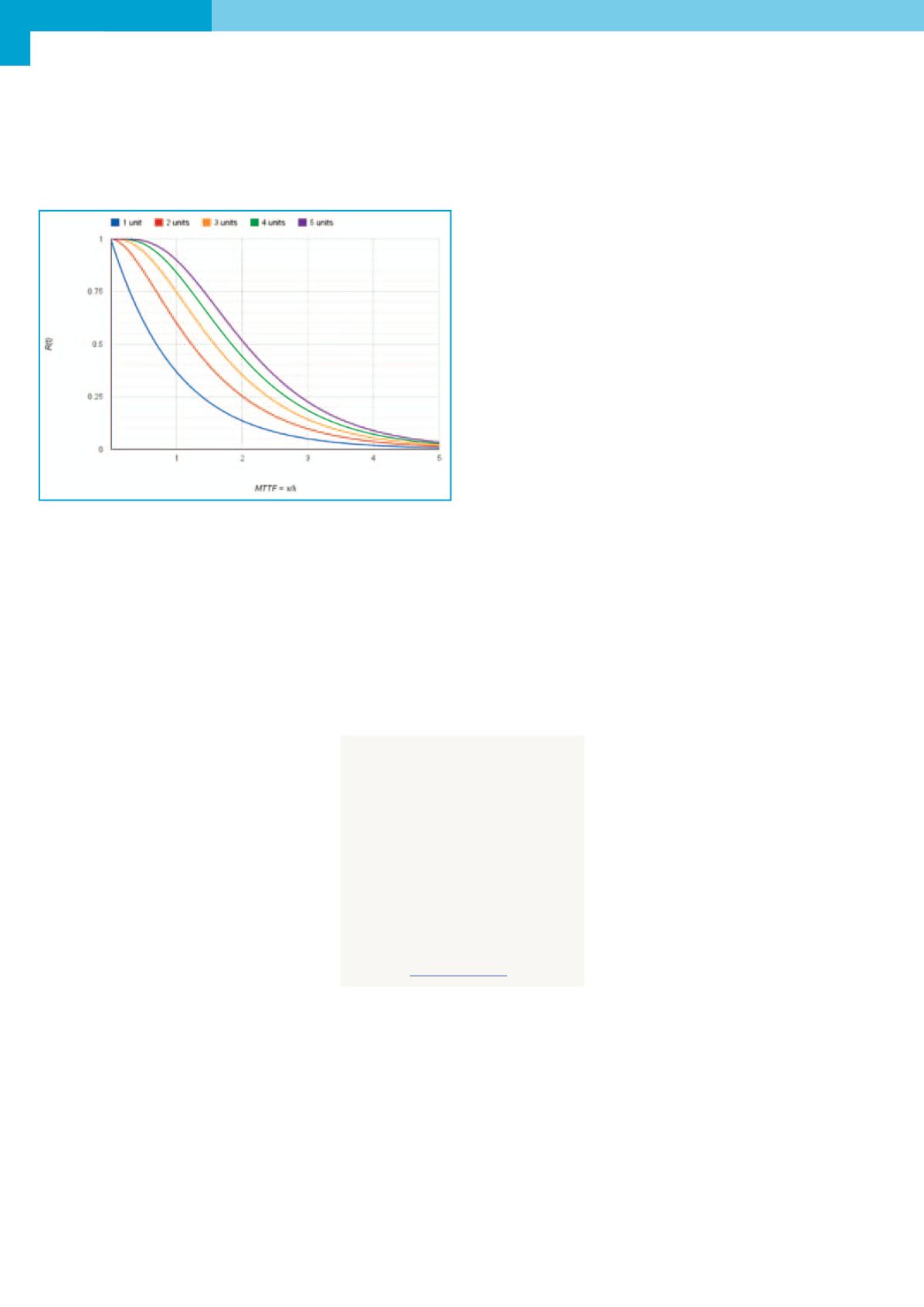
POWER
RELIABILITY
38
- ELETTRONICA OGGI 456 - SETTEMBRE 2016
getto ottimale tiene contro di questi fattori e prevede tutte le
necessarie azioni finalizzate a minimizzare la loro comparsa e
il loro impatto.
Le sollecitazioni di tipo termico possono essere di due tipi:
statiche e dinamiche. Le sollecitazioni termiche statiche, dove
gli alimentatori vengono fatti funzionare a elevate temperatura,
comportano il deterioramento dei componenti e dei materiali
che li costituiscono. I condensatori bulk (o meglio il liquido
elettrolitico) possono iniziare ad asciu-
garsi oppure la sigillatura può essere sot-
toposta a notevoli sollecitazioni, mentre
anche i rivestimenti dei resistori possono
iniziare a deteriorarsi e a rompersi. Le
aree di interconnessione e accoppiamen-
to possono espandersi e dar luogo a
fenomeni di disadattamento.
Le sollecitazioni dinamiche sono associa-
te a cicli di raffreddamento/riscaldamento
che provocano fenomeni di contrazione/
espansione responsabili del verificarsi di
micro-fratture.
La gravità delle sollecitazioni meccaniche
dipendono dalle modalità e dal luogo in
cui l’alimentatore verrà installato e fatto funzionare. Queste
sollecitazioni possono causare guasti di natura sia intermitten-
te sia permanente poiché le fratture che si sono sviluppate e i
collegamenti del circuito iniziano ad allargarsi e, in alcuni casi,
a ricomporsi.
Le sollecitazioni elettriche sono rappresentate da qualsiasi
tensione, corrente o altri parametri applicati al dispositivo.
Sollecitazioni eccessive si generano nel momento in cui un
componente viene fatto funzionare a valori superiori rispetto a
quelli nominali, a causa di una scelta poco oculata o a un even-
to specifico. Ad esempio la tensione nominale di un conden-
satore potrebbe essere 100 VDC ma durante il funzionamento
potrebbe verificarsi uno spike di tensione di 150 VDC.
Migliorare l’affidabilità di un alimentatore tramite
la progettazione…
Ovviamente il progetto e la topologia dovrebbe essere studiati
in maniera oculata garantendo un adeguato livello di affida-
bilità. È necessario tener conto di molti fattori come gli effetti
dei transitori della linea e del carico così come del rumore. Il
progettista deve inoltre determinare con attenzione i valori
minimi/massimi dei parametri dei componenti per garantire
un funzionamento affidabile (un valore tipico è praticamente
privo di significato), così come quelli dei parametri critici che
vengono considerati di minore importanza, come ad esempio
il coefficiente di temperatura di alcuni valori.
Si è già sottolineata la necessità di gestire le temperature ope-
rative, per cui l’analisi termica del progetto e la sua implemen-
tazione fisica sono aspetti critici.
La simulazione SPICE (Simulation Program with Integrated
Circuit Emphasis) o metodi analoghi di modellazione del pro-
getto sono operazioni essenziali, per cui è necessario utilizzare
modelli realistici e non semplificati dei componenti, delle sche-
de PCB e delle piste per la verifica delle prestazioni statiche e
dinamiche. Nella scelta dei componenti è necessario adottare
una strategia prudente, prevedendo margini aggiuntivi per i
valori sia iniziali sia di lungo termine per
molti dei valori delle loro specifiche. Inol-
tre nella stesura del layout è necessario
tener contro del fatto che molti alimen-
tatori devono gestire flussi di corrente di
notevole intensità, dell’ordine di 10, 20A o
ancora più elevati.
La fase successiva ala progettazione è la
scelta dei componenti specifici. Poiché
risulta praticamente impossibile distin-
guere un’unità di qualità scadente o con-
traffatta, la credibilità del produttore è
l’elemento chiave. I componenti, inoltre,
devono risultare compatibili con il pro-
cesso produttivo e bisogna prevede, lad-
dove richiesto, linguette di montaggio, punti di collegamento
di larghezza adeguata e conduttori “robusti” oppure morsetti
a vite.
Per consentire l’adozione delle metodologie DFM (Design For
Manufacturability), anche il processo di saldatura utilizzato
per la realizzazione dell’alimentatore deve essere preso in
considerazione. Mentre i profili di temperatura della saldatura
a riflusso sono chiaramente definiti, le normative relative ai
componenti e alla saldatura senza piombo (lead-free) preve-
dono un profilo differente per la saldatura a riflusso e tutti
CUI adotta le migliori proce-
dure per garantire la massima
affidabilità dei propri alimen-
tatori. Ulteriori informazioni
sui prodotti della società e
sulle modalità di utilizzo per
incrementare l’affidabilità dei
sistemi sono disponibili all’in-
dirizzo:
www.cui.comFig. 3 – Effetto della ridondanza sull’MTTF