Pickering Interfaces announces 3-pronged approach to obsolescence avoidance
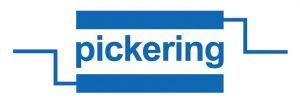
Pickering Interfaces announced the company’s formal approach to protecting customers from one of the most expensive challenges test engineers face when maintaining automated test equipment (ATE) – obsolescence.
“Mission-critical products with long lifecycles have components that need to be tested decades after they were manufactured and their initial test systems were designed,” said Keith Moore, CEO of Pickering. “When instrumentation providers discontinue components in those test systems – these companies, often in aerospace/defense, railway transportation, or power, are left stranded, trying to find a replacement or facing an imminent and costly test system redesign.”
Furthermore, in highly regulated industries like defense, changing significant components, software, or processes in a test system can trigger a demand for that test system to be re-certified, a process that can cost anywhere from $1M to $100M.
Pickering’s obsolescence strategy includes three key factors:
1. Planning for obsolescence during the design phase: Pickering engineering teams evaluate complete plans and anticipate upcoming industry challenges to ensure there’s a test solution to meet full demands.
2. Using standardized platforms: By supporting and maintaining more than 1000 PXI and LXI modules and thousands more iterated from those, Pickering offers standard solutions that are more easily evolved.
3. Ensuring ultra long-term support: Pickering commits to support modules designed into customer system for the entire product lifecycle, even redesigning modules when necessary.
If customers previously standardized on competitor platforms and now face obsolescence without a path forward, Pickering often can adapt modules to match form, fit, and function of the original hardware.